The Essential Guide to EP Coating: Techniques, Benefits, and Applications
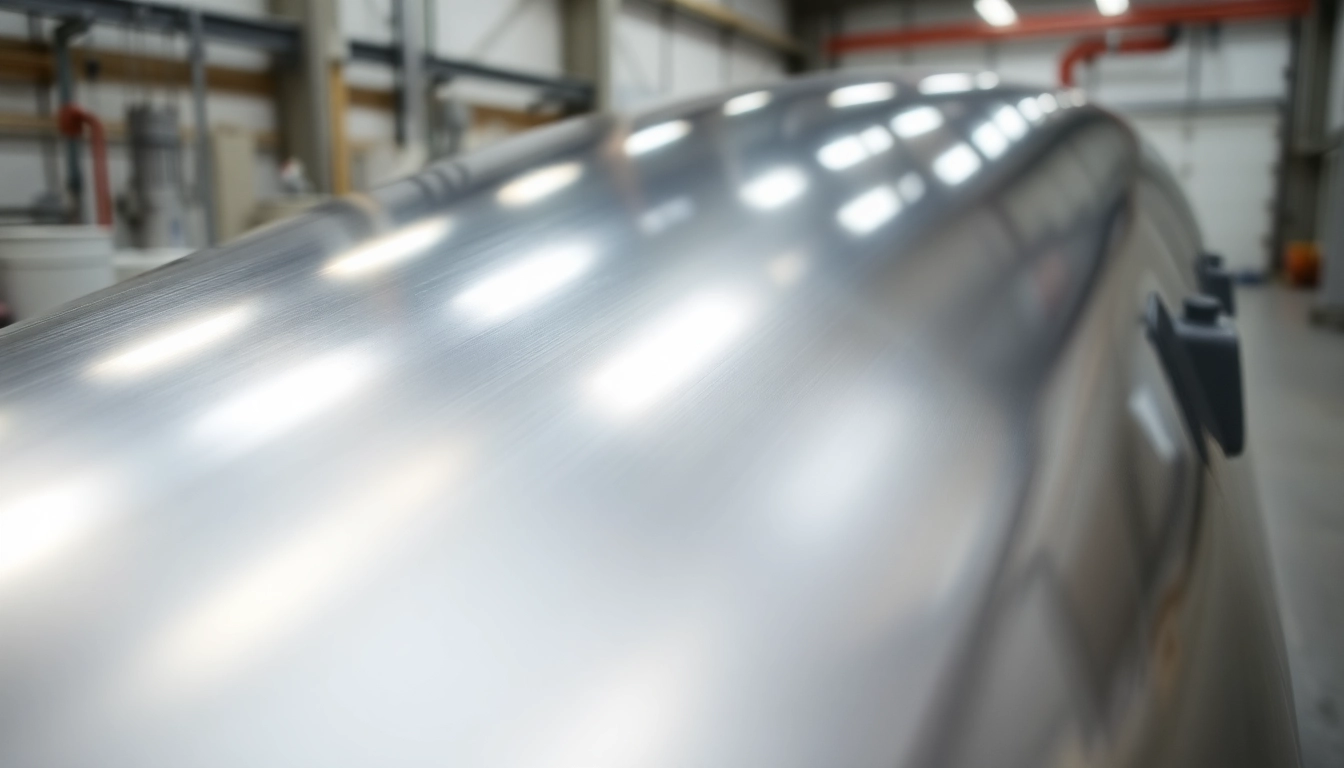
What is EP Coating?
Defining Electrophoretic Coating
Electrophoretic coating, commonly known as ep coating, is a sophisticated surface finishing technology utilized primarily for metal components. The process involves the application of a paint film through the use of electric current, allowing for a dense and uniform coating thickness. Popularly used in the automotive and industrial sectors, EP coating enhances the resistant properties of the substrate, particularly against corrosion and wear.
How EP Coating Works
EP coating operates through a process called electrophoretic deposition. The paint used is a suspension of polymer particles in a liquid medium, typically water-based. When an electric field is applied across the suspension, positively charged paint particles migrate towards negatively charged substrates, resulting in an even coating. This method ensures not only coverage of flat surfaces but also complex geometries, making it ideal for various applications.
Applications in Various Industries
EP coating finds applications across multiple industries, including:
- Automotive Industry: Widely used for parts such as chassis, body shells, and components exposed to harsh environmental conditions.
- Appliance Manufacturing: Used to coat domestic appliances like refrigerators and washing machines for aesthetic appeal and rust prevention.
- Electronics: Ensures protective layers on circuit boards and electronic components, enhancing their lifespan and reliability.
- Medical Equipment: Maintains hygiene and ensures durability on tools and devices used in healthcare.
Key Advantages of EP Coating
Durability and Corrosion Resistance
One of the primary benefits of EP coating is its exceptional durability. The coating is resistant to scratches, abrasions, and chemical exposure, which is particularly critical in harsh environments. Test data indicates that EP-coated substrates can withstand salt spray tests for over 1000 hours, showcasing their corrosion resistance.
Environmentally Friendly Process
In contrast to traditional solvent-based paints, EP coating is more environmentally friendly because it predominantly uses water-based solutions. The process generates minimal volatile organic compounds (VOCs), facilitating compliance with stringent environmental regulations while lowering the ecological footprint of manufacturing processes.
Cost-Effectiveness in Manufacturing
The efficiency of EP coating contributes to its cost-effectiveness. The automated application process reduces labor costs, while its high transfer efficiency minimizes paint waste—often quoted as exceeding 90%. Furthermore, the coating’s durability leads to reduced maintenance and replacement costs over time.
EP Coating Process Explained
Preparation of Metal Surfaces
Surface preparation is crucial for ensuring the effectiveness of the EP coating. Substrates must undergo de-greasing, phosphating, or sandblasting to remove impurities and create a suitable surface for adhesion. This step is vital for achieving optimal coating performance as poor preparation can lead to peeling or poor adhesion.
Electrophoresis Process Steps
The electrophoresis process consists of several key stages:
- Substrate Preparation: As previously mentioned, ensuring a clean and reactive surface.
- Submersion: The prepared component is immersed in a bath containing the electrophoretic paint.
- Electrophoresis Application: The electric current is applied, causing paint particles to migrate and deposit on the substrate surface in a uniform manner.
- Rinsing: Excess paint and residue are washed off to maintain coating integrity.
- Curing: The coated part is cured in an oven to enhance the durability and adhesion of the coating.
Post-Coating Curing
Curing is an essential final step in the EP coating process. It typically involves heating the coated components for a specified duration to ensure that the paint chemically bonds to the substrate. This step is crucial for achieving the desired finished properties, including resistance to chemicals and physical damage.
Comparison with Other Coating Methods
EP Coating vs. Powder Coating
While both EP coating and powder coating serve to protect and enhance the appearance of metal, they differ significantly in their application and properties:
- Application Method: EP coating uses an electric field to attract paint to the surface, while powder coating uses an electrostatic charge to apply dry powder which is then melted and cured.
- Thickness Control: EP coating allows more control over thickness, making it ideal for precision applications, whereas powder coating can be limited by the powder’s flow characteristics.
- Surface Compatibility: EP coating can be applied to metal substrates in various shapes and sizes, while powder coating may struggle with complex geometries due to powder clumping.
Benefits Over Traditional Paints
When compared to traditional liquid paints, EP coating offers various advantages:
- Uniform Coating Thickness: EP coating ensures even film thickness across surfaces, including complex shapes.
- Enhanced Adhesion: The electrophoretic process allows for superior adhesion to substrates, leading to longer-lasting finishes.
- Faster Application: The automated nature of electrophoretic systems can result in faster production rates compared to manual painting processes.
Applications in Automotive vs. Industrial Settings
In automotive applications, EP coating is used extensively for its corrosion resistance and aesthetic appeal, protecting components from rust and paint damage. Industrial settings leverage EP coating for machinery and equipment, where protective layers against abrasion, chemicals, and harsh environments are critical. While the methodologies may overlap, the requirements of automotive versus industrial applications can lead to different formulations and corrosion resistance metrics.
Future Trends in EP Coating Technology
Innovations in Coating Materials
The future of EP coating is promising, with ongoing research into innovative materials that can enhance performance. Advances in nanotechnology may lead to coatings with superior durable attributes, including enhanced scratch resistance and self-cleaning properties. Moreover, formulations that incorporate recycled materials are becoming increasingly popular, promoting sustainable practices.
Advancements in Application Techniques
The application of robotics and automation innovations is expected to enhance the efficiency and precision of EP coating processes. These advancements will not only improve the quality of coatings but also reduce variability in coating thickness and application time, ultimately leading to more streamlined manufacturing processes.
Market Growth and Industry Outlook
With an increasing emphasis on sustainability and eco-friendly practices, the demand for EP coating is projected to grow significantly in the coming years. Industries are increasingly opting for EP coatings for their efficient application processes and the ability to provide a high level of protection against environmental factors. Market analysts predict a steady growth rate as more companies adopt these technologies to meet regulatory standards and consumer expectations.
Leave a Comment