Mastering the Art of Welding: A Comprehensive Guide to the Unimig TIG Welder
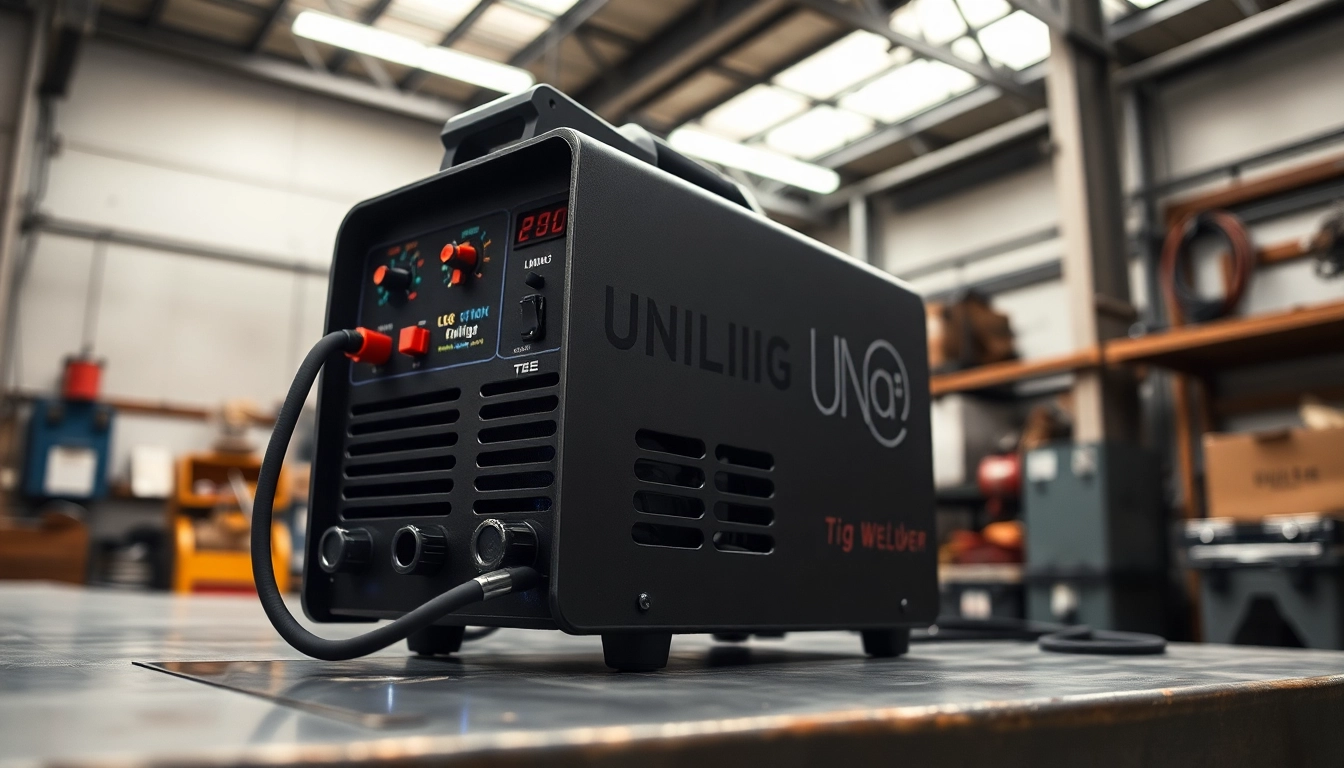
Understanding the Unimig TIG Welder
What is a TIG Welder?
TIG welding, or Tungsten Inert Gas welding, is a precise and versatile welding process that uses a non-consumable tungsten electrode to produce the weld. The process is known for its ability to create clean, strong welds in a variety of metals, including aluminum, stainless steel, and mild steel. Unlike MIG welding, which uses a wire electrode that melts to form the weld, TIG welding requires solid filler material to be added manually. This method allows for greater control over the weld and is preferred in applications where aesthetics and strength are crucial.
Key Features of Unimig TIG Welders
Unimig is renowned for its high-quality welding equipment, particularly its TIG welders. These machines feature several key advancements:
- High-Frequency Start: This feature allows for a stable arc initiation without the need for contact, minimizing tungsten contamination.
- AC/DC Capabilities: Unimig TIG welders, such as the Razor and Viper series, offer both alternating current (AC) and direct current (DC) options, making them suitable for welding different metals.
- Inverter Technology: Most Unimig TIG welders utilize inverter technology, providing excellent energy efficiency and consistent welding performance across a range of thicknesses.
- Portability: The compact and lightweight designs of these machines enhance their portability, making them ideal for on-site jobs.
- Adjustable Settings: Unimig TIG welders come equipped with various adjustment features to control settings such as arc length, amperage, and gas flow rate—allowing for customized welding experiences.
Applications of TIG Welding
TIG welding has a wide array of applications across various industries. It’s particularly valued in precision welding tasks where the aesthetic quality of the weld is paramount. Common applications include:
- Aerospace Industry: Used for welding components made from aluminum and titanium, materials that require excellent strength-to-weight ratios.
- Automotive Manufacturing: Ideal for creating custom exhaust systems and chassis parts, especially in high-performance and classic cars.
- Construction: Essential for welding stainless steel structures and frameworks due to its strong and clean welds.
- Artistic Projects: Artists and fabricators use TIG welding for sculptures and metal art due to the control it offers over the welding process.
Choosing the Right Unimig TIG Welder
Unimig Viper vs. Razor Models
When it comes to selecting the right Unimig TIG welder, understanding the differences between the Viper and Razor series is crucial.
The unimig tig welder models in the Viper series are designed with beginners in mind, featuring intuitive controls and helpful setup guides mounted on the machine itself. The Razor series, on the other hand, targets more advanced users and professionals, offering enhanced performance capabilities such as greater amperage ranges and more advanced features for industrial applications. The Razor series appeals particularly to users who need flexibility, robustness, and top-grade weld performance in more challenging applications.
Factors to Consider When Buying
Before purchasing a Unimig TIG welder, consider the following factors:
- Type of Materials: Ensure the welder is suitable for the materials you plan to work with, whether it’s stainless steel, aluminum, or magnesium.
- Power Output: Evaluate the machine’s amperage range. If you plan to weld thinner materials, a machine with lower amperage options may be more beneficial.
- Portability Needs: If you need to move your welder frequently, look for lightweight models that come with convenient carrying options.
- Budget: Define a budget considering the specifications and capabilities you require. Higher-end models often come with additional features that may or may not be essential for your needs.
Comparative Analysis of Price and Performance
While Unimig TIG welders are available at different price points, finding the right balance between performance and cost is critical. The Viper series typically ranges from around $1,299 for models like the VIPER MULTI 195 MAX to $1,649 for higher-end options like the VIPER TIG 180 AC/DC Mk II.
The Razor series, which offers advanced features, tends to be priced higher. The RAZOR TIG 200 AC/DC, for example, typically retails at about $1,714 due to its enhanced performance capabilities. Evaluating the performance requirements against your budget will help you make an informed choice, ensuring you’re neither overspending for unnecessary features nor opting for a model that doesn’t meet your needs.
Setting Up Your Unimig TIG Welder
Essential Accessories for Optimal Performance
Your Unimig TIG welder will perform best when equipped with the right accessories. Common accessories include:
- TIG Torch: Ensure you select a torch that is compatible with your welder model and suits the type of welding you’ll be performing.
- Electrodes and Filler Rods: Purchase appropriate tungsten electrodes and filler materials based on the materials being welded.
- Regulators and Flowmeters: These ensure the proper flow of shielding gas, which is critical in preventing contamination and oxidation.
- Protective Gear: Always invest in good quality welding helmets, gloves, and protective clothing to keep safe from sparks and harmful rays.
Step-by-Step Setup Guide
When setting up your Unimig TIG welder, follow this step-by-step guide to ensure everything is correctly installed:
- Unpack the Welder: Carefully remove the welding machine and all accessories from their packaging.
- Inspect Components: Check that all parts are in good condition and there are no visible damages.
- Set Up the TIG Torch: Connect the torch to the welder. Ensure you insert the tungsten electrode and tighten it properly.
- Attach the Gas Hose: Connect the shielding gas hose to both the TIG torch and gas cylinder, ensuring there are no leaks.
- Plug in the Welder: Connect your machine to the power source, ensuring the power supply is suitable for the machine’s requirements.
- Test the Setup: Before commencing work, perform a dry run to check all connections and settings. Adjust the gas flow and amperage based on your welding needs.
Troubleshooting Common Setup Issues
Some common issues during setup might include:
- Gas Leaks: If you suspect a gas leak, check all connections and replace damaged hoses.
- Improper Arc Start: This may result from a poorly set tungsten electrode or incorrect gas flow. Double-check these settings.
- Electrode Contamination: If the tungsten is contaminated, re-sharpen or replace it to avoid issues during welding.
Advanced Techniques for Unimig TIG Welders
Techniques for Welding Different Metals
Each metal type requires a unique approach when using a TIG welder. Here are some techniques for specific materials:
- Aluminum: Use AC current for aluminum welding. Adjust the balance control for cleaning and penetration based on material thickness.
- Stainless Steel: Utilize DC current to weld stainless steel. Ensure the tungsten is sharp, and set a lower amperage to avoid burning through.
- Mild Steel: DC current works best for mild steel, employing filler rods that match the type of mild steel being welded.
Utilizing Foot Pedals for Precision
A foot pedal significantly enhances control over the welding process. It allows the welder to adjust the amperage on the fly without halting the work. This is especially useful when welding various thicknesses or performing intricate tasks.
To maximize the effectiveness of using a foot pedal, practice gradually adjusting the pedal during different stages of your weld. This can help you develop a smooth, controlled technique that results in consistently high-quality welds.
Maximizing Efficiency and Quality
To get the most out of your Unimig TIG welder, consider the following best practices:
- Proper Material Preparation: Clean the base materials thoroughly to eliminate contaminants that could affect the weld.
- Control Travel Speed: Maintain a consistent and appropriate speed while welding to prevent issues such as burn-through or weak joints.
- Practice Welding Techniques: Continuous practice will enhance your skill level and efficiency over time.
Maintaining Your Unimig TIG Welder
Routine Maintenance Tips
Maintaining your Unimig TIG welder is essential for longevity and performance. Follow these routine maintenance tips:
- Clean After Use: Wipe down the exterior and check for any buildup of dust or debris inside the machine.
- Inspect Cables: Regularly check your power and gas cables for wear and tear, replacing them if necessary.
- Tungsten Replacement: Change your tungsten electrode regularly, especially after heavy use.
Common Problems and Solutions
Encountering issues with your welder can be frustrating, but many common problems can be quickly resolved:
- Inconsistent Arc: This can be caused by a dirty or improperly angled tungsten; reshaping or cleaning it can resolve this issue.
- Excessive Spatter: Often caused by incorrect settings, check your amperage and travel speed.
- Heat Issues: Ensure adequate cooling for your welder. Overheating can occur if the welder isn’t appropriately ventilated.
Extending the Lifespan of Your Welder
To prolong the life of your Unimig TIG welder, incorporate these strategies:
- Regular Professional Servicing: Consider having your machine serviced by professionals every couple of years.
- Use Protective Covers: When not in use, cover your welder to protect it from dust and potential damage.
- Store Appropriately: Keep your welder in a dry, cool place away from extreme temperatures or moisture.
Leave a Comment