Essential Thermal Management Materials for Effective Heat Dissipation in Electronics
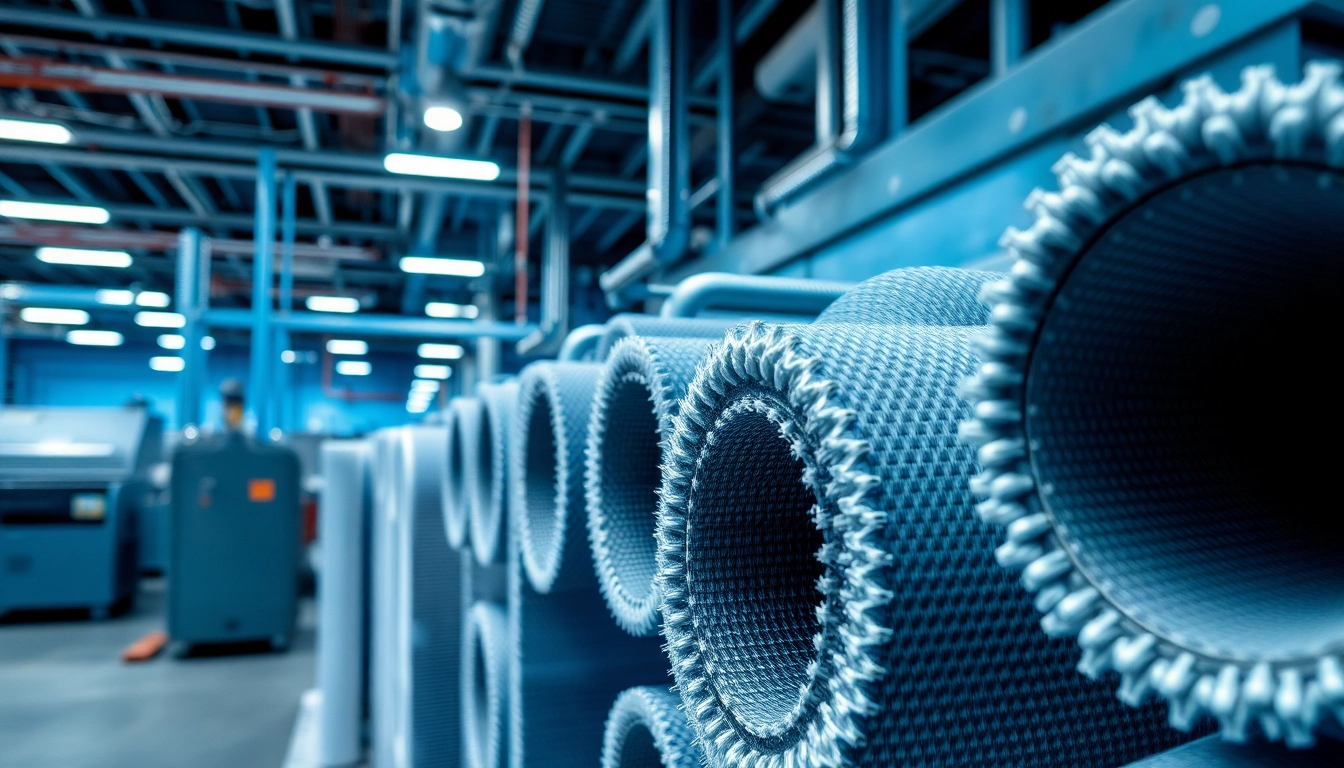
Understanding Thermal Management Materials
In the realm of electronics and heat management, thermal management materials play a pivotal role. They are tailored substances designed to effectively dissipate heat from critical components in various applications, ensuring optimal performance and longevity of devices. With the proliferation of electronic devices, the importance of selecting the right thermal management materials cannot be overstated. This article will dive into the fundamentals of these materials, their applications, best practices for selection, innovations in the field, and future trends.
What Are Thermal Management Materials?
Thermal management materials encompass a variety of substances used to control the heat produced by electronic devices. Typically, these materials function to either conduct, insulate, or dissipate heat, making them essential in preventing overheating and ensuring thermal stability. They are primarily categorized into several types, including thermal interface materials (TIM), thermal pads, phase change materials (PCM), heat sinks, and adhesives.
The Importance of Heat Dissipation
Heat management is a critical aspect of electronic design and engineering. As electronic components operate, they generate heat, and if not adequately managed, this can lead to reduced performance, component failure, and a shorter lifespan for devices. Efficient heat dissipation ensures that devices operate within their optimal temperature range, enhancing reliability and functionality.
Furthermore, as devices become smaller and more powerful, the challenge of controlling heat becomes increasingly complex, necessitating advanced thermal management solutions.
Types of Thermal Management Materials
Thermal management materials come in various types, each designed for specific applications and requirements. Understanding these materials is essential for making informed decisions about their application.
- Thermal Interface Materials (TIM): These materials are placed between heat-generating components and heat dissipation structures (like heat sinks) to enhance thermal conductivity. They fill microscopic gaps and voids, improving heat transfer efficiency.
- Thermal Pads: These are compliant, soft materials that conform to surfaces, facilitating thermal conductivity. They are primarily used in electronics to manage heat between chips and their cooling solutions.
- Phase Change Materials (PCM): These materials absorb, store, and release thermal energy during phase transitions, making them ideal for thermal regulation in applications where temperature stability is critical.
- Heat Sinks: Although not a material per se, heat sinks often incorporate thermal management materials to enhance heat dissipation. They are typically made from metals like aluminum or copper due to their high thermal conductivity.
- Thermal Greases and Adhesives: These are often used to bond components together while improving thermal transfer. They are particularly useful in situations where TIMs might not provide adequate conductivity.
Key Applications of Thermal Management Materials
Thermal management materials find applications across various sectors, owing to their crucial role in heat dissipation and thermal stability. Understanding these applications can aid in selecting the right materials for specific needs.
Electronics Cooling Solutions
The electronics industry relies heavily on thermal management materials to maintain device performance. Heat generated by processors, GPUs, and other components must be efficiently dissipated to avoid thermal throttling. Solutions such as thermal pastes and heat spreaders are commonly employed to enhance the efficiency of heat sinks. Advances in materials science have led to the creation of high-conductivity thermal interface materials that significantly improve thermal transfer efficiency, enabling more powerful and compact devices.
Aerospace and Automotive Applications
Aerospace and automotive industries also utilize thermal management materials to ensure operational safety and performance reliability under extreme conditions. Components in these sectors often face high thermal loads and varying environmental conditions, necessitating robust thermal management solutions. For instance, thermal pads and encapsulants are often employed to protect sensitive electronics in aircraft and vehicles from heat-induced failures.
Telecommunications Technology
In the telecommunications sector, effective heat management is required to ensure the reliability of equipment such as servers, routers, and communication devices. As these devices handle significant data loads, the associated heat must be managed effectively to prevent overheating and maintenance issues. Companies utilize a variety of thermal management materials, from gel-filled pads to advanced heat pipes, to maintain optimal temperatures for these critical systems.
Best Practices for Selecting Thermal Management Materials
Choosing the right thermal management materials is crucial for achieving optimal thermal performance and device longevity. Below are some best practices for material selection.
Evaluating Thermal Conductivity Performance
When selecting thermal management materials, the foremost consideration is their thermal conductivity. A material with high thermal conductivity will effectively transfer heat away from critical components, improving overall performance. Conductivity ratings, often expressed in watts per meter-kelvin (W/mK), should be evaluated in the context of the specific application, as many materials offer varying conductivity depending on thickness and application method.
Considerations for Material Durability
Ductility, thermal cycling resistance, and environmental stability are essential qualities of effective thermal management materials. In high-heat scenarios, materials may degrade over time, necessitating a closer look at durability. For instance, silicone-based materials offer excellent thermal stability but may not perform adequately in extreme environments; thus, materials should be chosen based on their expected lifespan and the specific conditions they will face.
Cost-Effectiveness in Material Choice
While high-performance thermal management materials may come with a premium price, it’s essential to consider the overall costs associated with system failure due to inadequate thermal management. A more cost-effective solution now might lead to higher long-term expenditures due to repairs, replacements, or unscheduled downtime. Therefore, cost analyses should include both upfront costs and potential long-term savings.
Innovations in Thermal Management Technologies
The thermal management materials industry is continually evolving with advancements in technology and materials science. Keeping abreast of these innovations can help businesses remain competitive and compliant with industry trends.
Recent Advances in Thermal Interface Materials (TIM)
Recent developments in TIMs have generated materials that not only enhance thermal conductivity but also offer additional benefits such as flexibility and ease of application. Innovations in graphene and carbon-based materials have resulted in products that exhibit superior thermal management capabilities while reducing the thickness and weight compared to traditional materials.
Emerging Trends in Thermal Solutions
There is a notable trend towards the integration of smart technologies and IoT in thermal management. Sensors that monitor temperature and adjust cooling mechanisms in real-time are becoming increasingly common. These innovations can significantly extend the life of electronic components and improve energy efficiency by adapting cooling processes based on operational demand.
Case Studies of Successful Implementations
Taking a look at case studies can provide additional insights into effective thermal management strategies. For example, companies like DuPont have successfully implemented phase change materials in consumer electronics, enhancing the device’s operational stability. Another case involves aerospace applications, where new thermal materials have been used to enhance the thermal resilience of avionics systems, leading to improved safety and performance metrics.
Future Trends in Thermal Management
Looking ahead, several key trends are poised to shape the future of thermal management materials and technologies.
The Role of Sustainable Materials
As the global focus shifts towards sustainability, the demand for environmentally friendly thermal management materials is on the rise. Manufacturers are exploring biocompatible and recyclable materials that reduce the overall environmental footprint of electronic devices. Innovations in bio-based thermoplastics and composites that provide robust thermal management while being less harmful to the planet will likely become more widespread.
Integration of Smart Technologies in Heat Management
The integration of artificial intelligence and machine learning will revolutionize thermal management systems. Smart materials capable of adaptive heat responses, combined with algorithms that predict thermal behavior, can drastically improve efficiency and reliability in electronics. Real-time data analytics will also enable manufacturers to optimize designs in ways previously unimaginable.
Predictions for Market Growth and Innovation
Market analysts project significant growth in the thermal management materials market, driven by the increasing demand for efficient heat management solutions across various industries. Innovations will continue to flourish as manufacturers aim to meet evolving consumer demands for reliability, efficiency, and sustainability, setting the stage for new entrants and disruptive technologies in the coming years.
Leave a Comment